A processing plant is similar to the human body; each system within needs to function properly both together and independently from other systems to be healthy.
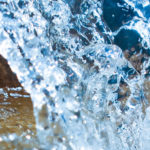
1. Tracking Inlet Water Conductivity
Ion exchange resins have a finite capacity, so the amount of conductivity in the water directly affects their ability to remove contaminants. Since higher conductivity leads to lower throughput (and vice versa), and conductivity varies widely during any given year, you should make sure you diligently track inlet conductivity and know that your system is prepared to meet throughput targets despite inlet conductivity variability.
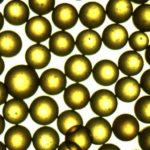
2. Maintaining Ion Exchange Resins
Understanding the current health, fouling levels and age of the resin along with system configuration can help you determine if the resin is capable of producing the throughput you need for the plant. Resin fouls as it collects contaminants in the inlet water, which will definitely affect throughput capacity. However, declining throughput capacity does not equal “dead” resin. Resin that is inherently healthy can be restored through effective cleaning which can boost resin capacity and throughput.
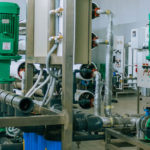
3. Maximizing Equipment Capability
A system can achieve its best performance and consistency with proper maintenance of key water system equipment and controls. It’s imperative to monitor equipment capability on a set and proactive maintenance schedule. As equipment deteriorates over time, many systems are unable to achieve the right frequency and necessary maintenance to run at their best.
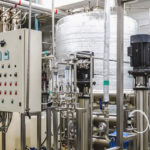
4. Optimize Regeneration Procedures
Reviewing and recalibrating regen procedures is also another important regular task for any system’s manager. While most systems are designed with specific instructions for performing regens, as time progresses, many of the established procedures change for various reasons including equipment and personnel changes, regen chemical changes and, at times, budget issues. Without checking on procedures, managers could find that regens are taking longer than necessary or the performance of the resin is being shortchanged by migrating procedure changes.
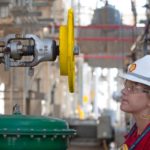
5. Improve Operator Performance
The methods operators use to run water systems can have an effect on the system’s effectiveness and efficiency, so it’s important for operators to be trained regularly. A comparison of written procedures and physical daily procedures should also be conducted with any differences noted and addressed.
Best Practices (PDF)
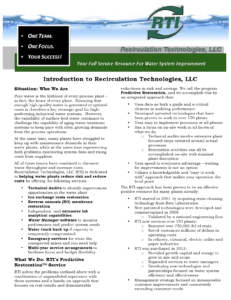
Save with RTI
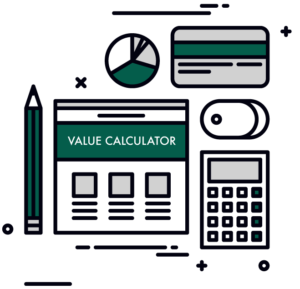
Our Services
Your Full Service Resource For Water System Improvement!
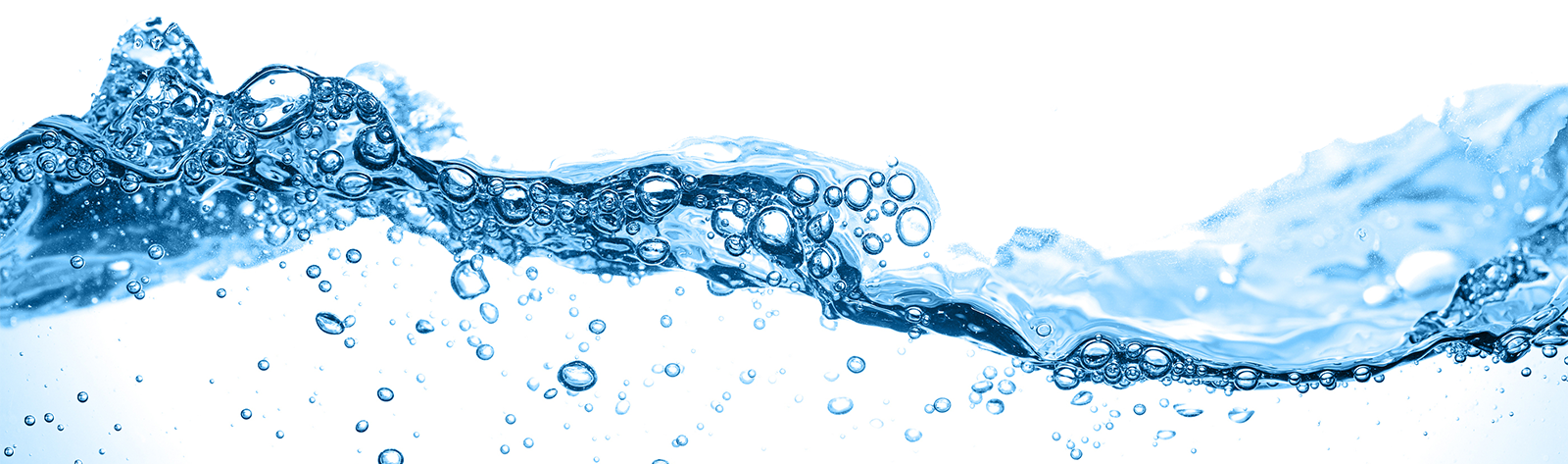